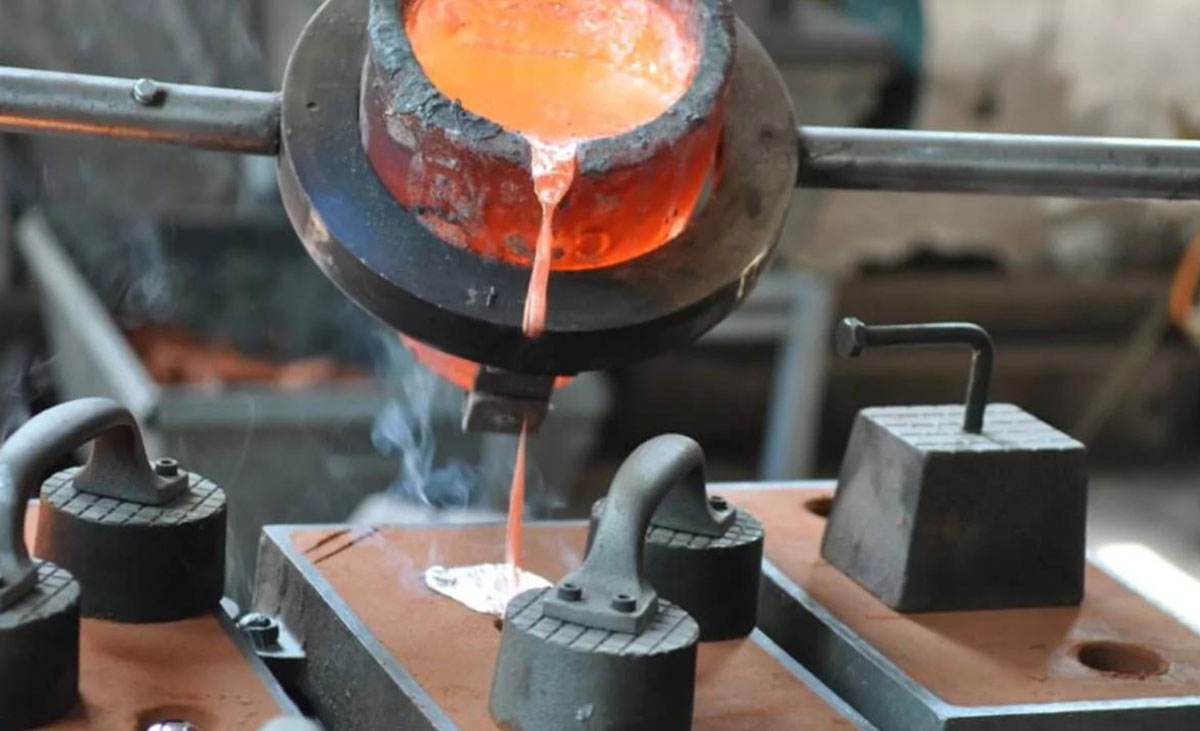
Die casting is a popular manufacturing process used to produce high-precision metal parts, particularly for industries like automotive, aerospace, and electronics. However, like any manufacturing technique, die casting can encounter various defects that impact the quality of the finished product.
Understanding these common issues and knowing how to prevent them can help manufacturers improve product consistency and reduce costly rework.
Porosity
Porosity refers to the presence of air pockets or voids within a die-cast part, which can compromise its strength and integrity. This defect can occur due to trapped gas during the injection process or improper cooling rates.
Prevention Tips:
- Optimize the injection speed and pressure to ensure a smooth and consistent flow of molten metal into the mold.
- Improve venting to allow gases to escape, preventing their entrapment in the part.
- Use degassed metal to reduce the likelihood of gas formation during the casting process.
- Control cooling rates to allow for uniform solidification and minimize the formation of voids.
Misalignment
Misalignment occurs when the mold halves are not properly aligned, leading to defects such as flash (excess metal) or dimensional inaccuracies. Misalignment can result from worn dies, poor maintenance, or improper machine setup.
Prevention Tips:
- Regularly maintain dies and machines to ensure they are properly aligned and functioning smoothly.
- Inspect mold alignment before each cycle, ensuring all components are properly positioned.
- Use advanced die-casting machines with automatic alignment mechanisms to reduce human error and improve consistency.
Cold Shut
A cold shut happens when the molten metal from two or more different parts of the mold fails to meet properly, resulting in a visible line or seam. This issue often arises due to insufficient metal flow or poor mold design.
Prevention Tips:
- Increase the injection speed and pressure to ensure a smooth, continuous flow of metal into the mold.
- Modify the mold design to optimize the flow path, ensuring that the molten metal can reach all areas without cooling too rapidly.
- Maintain consistent metal temperature to prevent premature solidification at the mold entrance.
Flash
Flash is the excess metal that spills over into areas outside the desired mold cavity. This occurs when the mold halves do not seal tightly or when there is excessive pressure during injection. Flash can cause dimensional issues and additional machining work to remove.
Prevention Tips:
- Ensure proper mold sealing to minimize gaps between the mold halves.
- Control injection pressure to avoid overfilling the mold.
- Optimize the gating system to direct metal flow more efficiently and prevent excessive pressure buildup.
Surface Defects
Surface defects, such as rough surfaces, die marks, or defects from slag contamination, can negatively affect the aesthetic and functional properties of a part. These defects can be caused by poor die maintenance, incorrect mold temperature, or insufficient metal filtration.
Prevention Tips:
- Regularly clean the die cavity to prevent the buildup of contaminants that can affect the surface finish.
- Maintain proper mold temperature to ensure a smooth metal flow and minimize die marks.
- Use filters to remove impurities from the molten metal before injection, preventing slag and other contaminants from damaging the part’s surface.
Dimensional Inaccuracies
Die-cast parts often require tight tolerances, and dimensional inaccuracies can arise due to thermal expansion, misalignment, or improper die design. These inaccuracies can make parts unusable or require extensive rework.
Prevention Tips:
- Use precise mold design and machining to ensure accurate part dimensions.
- Monitor and control the cooling rate to reduce distortion from thermal stresses.
- Regularly calibrate equipment to maintain tight tolerance control throughout the production process.